In heavy-duty applications, the reliability and durability of commercial hydraulic pumps are paramount. These robust pumps are designed to withstand the rigors of demanding industrial settings, ensuring continuous operation and minimizing costly downtime. In this comprehensive guide, we will explore the significance of unmatched reliability and durability in commercial hydraulic pumps for heavy-duty applications. By understanding their key components, functionalities, and the importance of regular maintenance, businesses can make informed decisions to maximize performance, extend the lifespan of their hydraulic pumps, and achieve long-term success and cost savings. Let’s delve into the world of commercial hydraulic pumps engineered for heavy-duty applications.
Understanding Commercial Hydraulic Pumps
Commercial hydraulic pumps are essential mechanical devices designed to generate and control hydraulic energy in heavy-duty applications. These pumps play a critical role in various industries, including manufacturing, construction, mining, and marine operations. Understanding the key aspects of commercial hydraulic pumps is crucial for ensuring their effective utilization. Here are the key points to comprehend:
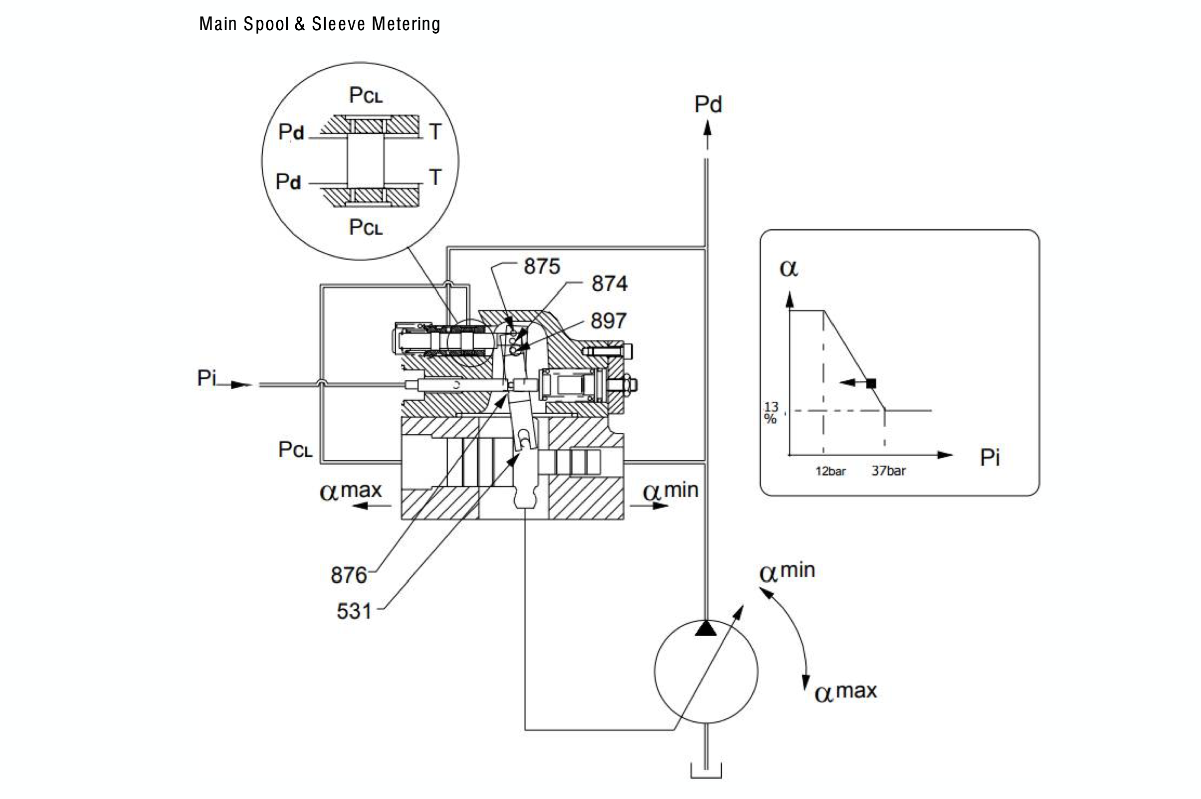
- Definition and Purpose: Commercial hydraulic pumps are mechanical devices that convert mechanical power into hydraulic energy. They act as the heart of hydraulic systems, providing the force necessary to move fluids and operate various hydraulic components such as cylinders, motors, and valves.
- Role in Heavy-Duty Applications: Commercial hydraulic pumps find extensive use in heavy-duty applications where high pressure and power are required. These applications include lifting heavy loads, powering construction equipment, operating hydraulic presses, and facilitating precise movements in industrial machinery.
- Key Components and Functionalities: Commercial hydraulic pumps consist of several essential components. The primary components include an electric motor or an engine that drives the pump, a pump body that houses internal components, pistons or vanes responsible for generating hydraulic pressure, and valves that control the flow direction and pressure within the system. These components work in harmony to ensure the efficient transmission of hydraulic power.
Commercial hydraulic pumps come in various types, such as gear pumps, vane pumps, and piston pumps. Each type offers distinct advantages depending on the specific application requirements, including flow rate, pressure capacity, and efficiency.
Understanding the fundamental aspects of commercial hydraulic pumps provides a solid foundation for selecting the appropriate pump for heavy-duty applications. By considering factors such as flow requirements, pressure capacities, and efficiency, businesses can optimize their hydraulic systems and ensure reliable and efficient power transmission in demanding industrial environments.
The Importance of Reliability in Heavy-Duty Applications
Reliability is of utmost importance when it comes to commercial hydraulic pumps used in heavy-duty applications. These demanding industrial settings require pumps that can operate continuously, withstand extreme conditions, and deliver consistent performance. Here are the key reasons why reliability is critical in heavy-duty applications:
- Continuous Operation: In heavy-duty industries, any interruption or downtime can have severe consequences, leading to production delays, financial losses, and potential safety hazards. Reliable hydraulic pumps ensure continuous operation, allowing businesses to meet deadlines, maintain productivity, and avoid costly disruptions.
- Minimizing Downtime: Unplanned downtime due to pump failures can result in significant financial losses. Reliable hydraulic pumps, built with robust materials and advanced technologies, minimize the risk of sudden breakdowns, reducing the likelihood of costly repairs and lengthy downtime. This improves overall operational efficiency and helps businesses stay on schedule.
- Enhanced Safety Measures: Heavy-duty applications often involve high loads, challenging environments, and stringent safety requirements. Reliable hydraulic pumps play a vital role in ensuring the safe operation of machinery and equipment. By providing consistent and controlled power transmission, these pumps help prevent accidents, protect personnel, and maintain a safe working environment.
- Preventing Costly Failures: Hydraulic pump failures can lead to extensive damage not only to the pump itself but also to other connected hydraulic components and machinery. Reliable pumps, designed with durability in mind, minimize the risk of catastrophic failures, reducing repair and replacement costs. This translates into long-term cost savings for businesses.
Investing in reliable hydraulic pumps specifically designed for heavy-duty applications is essential for businesses seeking consistent performance, productivity, and cost-efficiency. By prioritizing reliability, businesses can mitigate risks, ensure uninterrupted operation, and maintain a competitive edge in their respective industries.
Durability: Key to Longevity and Cost Savings
Durability is a critical factor in commercial hydraulic pumps used in heavy-duty applications. These pumps must withstand harsh operating conditions, resist wear and tear, and maintain their performance over an extended period. Here’s why durability is key to longevity and cost savings in heavy-duty applications:
- Resisting Wear and Tear: Heavy-duty applications subject hydraulic pumps to extreme pressures, high loads, and challenging environments. Durability ensures that pumps can withstand these demanding conditions without experiencing premature wear and damage. Robust construction, high-quality materials, and advanced engineering techniques contribute to the longevity of hydraulic pumps.
- Cost Savings through Reduced Maintenance and Replacement: Durable hydraulic pumps require less frequent maintenance and replacement, resulting in cost savings for businesses. When pumps are built to withstand the rigors of heavy-duty applications, they experience fewer failures and breakdowns. This reduces the need for costly repairs, replacement parts, and downtime, leading to improved operational efficiency and lower maintenance costs.
- Reliable Performance over Time: Durability directly affects the overall performance of hydraulic pumps. By maintaining their performance characteristics over an extended period, durable pumps ensure consistent and reliable operation. This reliability minimizes disruptions in heavy-duty applications, allowing businesses to meet production targets, reduce delays, and avoid additional costs associated with unscheduled downtime.
- Longevity and Return on Investment (ROI): Durability extends the lifespan of hydraulic pumps, maximizing the return on investment. When pumps are designed and built to be durable, they can provide reliable performance for a longer period, reducing the frequency of replacements and the associated costs. This extends the pump’s service life, enhances profitability, and improves the overall cost-effectiveness of heavy-duty operations.
Investing in durable hydraulic pumps specifically designed for heavy-duty applications is a strategic choice for businesses aiming for longevity, cost savings, and optimized performance. By selecting pumps known for their durability, businesses can minimize maintenance requirements, reduce downtime, and achieve a higher return on investment over the lifespan of the pumps.
Features of Commercial Hydraulic Pumps for Heavy-Duty Applications
Commercial hydraulic pumps designed for heavy-duty applications possess specific features that enable them to withstand demanding environments and deliver reliable performance. These features ensure the efficient transmission of hydraulic power and contribute to the overall effectiveness of hydraulic systems. Here are the key features of commercial hydraulic pumps for heavy-duty applications:
- High-Performance Materials and Construction: Hydraulic pumps for heavy-duty applications are constructed using high-quality materials such as cast iron, steel alloys, and hardened components. These materials provide excellent strength, durability, and resistance to wear and corrosion. The robust construction ensures the pump can withstand the challenging conditions present in heavy-duty industrial environments.
- Robust Designs to Withstand Challenging Environments: Commercial hydraulic pumps designed for heavy-duty applications incorporate robust designs that can endure extreme temperatures, vibrations, and high-pressure environments. Reinforced housing, strengthened mounting points, and vibration-damping mechanisms enhance the pump’s ability to withstand challenging conditions, minimizing the risk of failures or damage.
- Advanced Sealing Mechanisms for Enhanced Reliability: Hydraulic pumps in heavy-duty applications require reliable sealing to prevent leaks and maintain optimal performance. Commercial hydraulic pumps employ advanced sealing mechanisms such as high-quality seals, gaskets, and O-rings. These seals are specifically designed to withstand high pressures, resist fluid leakage, and maintain consistent performance over time.
- Precise Control and Flow Regulation: Heavy-duty applications often require precise control over hydraulic power transmission. Commercial hydraulic pumps feature advanced control mechanisms, including adjustable flow control valves, pressure compensators, and proportional controls. These features allow operators to regulate the flow rate and pressure of hydraulic fluid accurately, ensuring precise and efficient power delivery.
- Protection Against Contaminants: In heavy-duty applications, hydraulic systems are exposed to various contaminants, such as dust, debris, and moisture. Commercial hydraulic pumps incorporate protective measures, including filters, breathers, and contamination-resistant components. These features help to maintain the cleanliness of the hydraulic fluid, prevent damage to the pump, and extend its lifespan.
The combination of these features ensures that commercial hydraulic pumps for heavy-duty applications can deliver reliable performance, withstand challenging environments, and provide long-lasting operation. By selecting pumps with these specific features, businesses can ensure the efficiency and effectiveness of their hydraulic systems, minimizing downtime, and maximizing productivity in demanding industrial settings.
Maintaining Optimal Performance and Extending Lifespan
To maintain optimal performance and extend the lifespan of commercial hydraulic pumps used in heavy-duty applications, regular maintenance practices and proper care are essential. By following maintenance guidelines and implementing effective strategies, businesses can ensure the longevity and reliability of their hydraulic pumps. Here are key considerations for maintaining optimal performance and extending the lifespan of commercial hydraulic pumps:
- Regular Maintenance Practices: Establish a routine maintenance schedule for hydraulic pumps and adhere to it consistently. Regular maintenance includes inspections, cleaning, lubrication, and component replacements as needed. This proactive approach helps identify and address potential issues before they escalate into major problems, minimizing the risk of unexpected failures and costly downtime.
- Inspection and Troubleshooting Techniques: Conduct thorough inspections of hydraulic pumps to identify any signs of wear, leaks, or abnormal operation. Monitor factors such as fluid levels, pressure readings, and noise/vibration levels. Troubleshoot and address issues promptly to prevent further damage and maintain optimal performance. Utilize diagnostic tools and equipment, and consult manufacturer guidelines for proper inspection procedures.
- Lubrication and Fluid Management Considerations: Proper lubrication is crucial for the smooth operation of hydraulic pumps. Follow manufacturer recommendations for lubrication intervals and use high-quality lubricants suitable for heavy-duty applications. Monitor fluid levels and quality regularly, and perform fluid analysis to identify potential contamination or degradation. Regularly replace or filter hydraulic fluid as needed to maintain cleanliness and preserve pump performance.
- Component Replacement and Repair: Over time, certain components in hydraulic pumps may wear out or become damaged. Timely replacement or repair of worn or faulty components is essential to prevent further damage and maintain pump performance. Follow manufacturer guidelines and use genuine replacement parts to ensure compatibility and optimal functionality.
- Operator Training and Best Practices: Provide comprehensive training to operators and maintenance personnel on proper pump operation, maintenance procedures, and safety protocols. Emphasize best practices for pump usage, such as avoiding excessive loads, maintaining proper pressure levels, and operating within specified parameters. Educate personnel on the importance of regular maintenance and encourage reporting of any abnormalities or concerns.
By implementing these maintenance practices and strategies, businesses can optimize the performance of commercial hydraulic pumps and extend their lifespan. Regular maintenance ensures that pumps operate at their best, minimizing the risk of failures and costly downtime. Additionally, proper care and attention contribute to the overall efficiency and effectiveness of hydraulic systems, maximizing productivity and cost-effectiveness in heavy-duty applications.
Choosing the Right Pump for Heavy-Duty Applications
Selecting the right commercial hydraulic pump is crucial for ensuring optimal performance and reliability in heavy-duty applications. With various options available in the market, it’s important to consider several factors to make an informed decision. Here are key considerations for choosing the right pump for heavy-duty applications:
- Application Requirements: Understand the specific requirements of your heavy-duty application. Consider factors such as flow rate, pressure capacity, operating conditions, and the nature of the tasks the pump will be performing. This information will help determine the appropriate pump size, power, and capabilities needed for efficient operation.
- Compatibility: Ensure that the chosen pump is compatible with your existing hydraulic system and components. Consider factors such as fluid compatibility, fitting sizes, and interface requirements. The pump should seamlessly integrate into your system without the need for extensive modifications or additional adapters.
- Efficiency and Power: Evaluate the efficiency and power characteristics of the pump. Look for pumps that offer high volumetric efficiency, minimizing energy waste and maximizing power transmission. Consider the power requirements of your heavy-duty application and select a pump that can meet or exceed those requirements.
- Load Capacity and Durability: Heavy-duty applications often involve high loads and demanding conditions. Choose a pump that can handle the expected loads and has a durable construction to withstand the challenges of the application. Look for pumps made from robust materials and designed for heavy-duty operations.
- Manufacturer Reputation and Support: Research the reputation and track record of the pump manufacturer. Consider factors such as their experience, industry expertise, and customer reviews. A reputable manufacturer will offer reliable products, technical support, and readily available spare parts, ensuring long-term support and minimizing downtime.
- Cost Considerations: While upfront cost is a factor, consider the overall cost-effectiveness of the pump over its lifespan. Assess the pump’s durability, maintenance requirements, and energy efficiency. Conduct a cost-benefit analysis that takes into account factors such as energy savings, reduced maintenance needs, and potential productivity gains.
By carefully considering these factors and consulting with hydraulic experts or manufacturers, businesses can choose the right commercial hydraulic pump for heavy-duty applications. A well-matched pump ensures efficient power transmission, durability, and long-term reliability, ultimately maximizing productivity and minimizing operational costs.
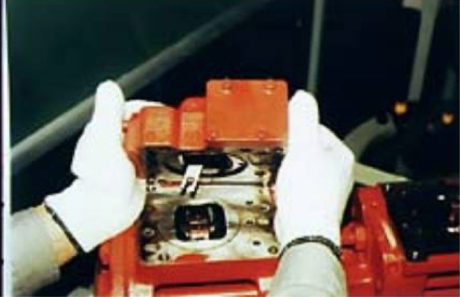
Conclusion
In conclusion, the unmatched reliability and durability of commercial hydraulic pumps are crucial for heavy-duty applications. These pumps ensure continuous operation, minimize downtime, and enhance safety measures in demanding industrial settings. By selecting pumps with robust designs, high-quality materials, and advanced sealing mechanisms, businesses can rely on their performance and avoid costly failures.
Durability is key to achieving longevity and cost savings in heavy-duty applications. Durable hydraulic pumps resist wear and tear, reducing maintenance and replacement needs. They provide reliable performance over time, minimizing disruptions and optimizing operational efficiency.
When choosing a hydraulic pump for heavy-duty applications, consider factors such as application requirements, compatibility, efficiency, power, load capacity, and the reputation of the manufacturer. Making an informed decision ensures the pump is suited to the specific demands of the application, maximizing performance and minimizing downtime.
Regular maintenance practices, such as inspections, lubrication, and component replacements, are crucial for maintaining optimal pump performance and extending its lifespan. By following manufacturer guidelines, implementing best practices, and providing operator training, businesses can optimize the performance of commercial hydraulic pumps and maximize their longevity.
Investing in reliable and durable commercial hydraulic pumps tailored for heavy-duty applications is a strategic choice that ensures long-term success, cost savings, and optimized performance. By prioritizing the importance of unmatched reliability and durability, businesses can ensure efficient power transmission, minimize downtime, and maintain a competitive edge in heavy-duty industrial environments.
Related Keywords
# Commercial Intertech pump catalog,
# Parker Commercial Intertech,
# Commercial Hydraulics Kontak Ltd,
# Commercial hydraulic valve BANK,
# Commercial Intertech hydraulic pump,
# Commercial Intertech hydraulic cylinders,
# Commercial Intertech valve Parts,
# Commercial Hydraulics Kontak grantham ENGLAND,