Dump hydraulic pumps are essential components used in various industries for efficient hydraulic systems. These pumps play a crucial role in powering the movement of hydraulic fluids, enabling the operation of heavy machinery and equipment. By converting mechanical energy into hydraulic energy, dump hydraulic pumps facilitate the smooth and controlled transfer of fluids, enhancing productivity and performance. Whether in construction, manufacturing, or agriculture, the reliable operation of dump hydraulic pumps is vital for achieving optimal efficiency and minimizing downtime. In this comprehensive guide, we will explore the different types of dump hydraulic pumps, their configurations, selection criteria, and best practices for maintenance and performance optimization.
Overview of Hydraulic Pump Systems
Hydraulic systems are widely used in various industries due to their ability to transmit power efficiently and precisely. These systems consist of several key components, with hydraulic pumps being one of the most crucial elements. Hydraulic pumps are responsible for generating the necessary fluid flow and pressure required to drive the system. They function by converting mechanical energy into hydraulic energy, utilizing various principles and mechanisms.
In a hydraulic system, the pump draws hydraulic fluid from a reservoir and delivers it under pressure to the rest of the system. This pressurized fluid is then used to operate cylinders, motors, or other hydraulic devices, allowing for controlled movement and force generation. The pump essentially acts as the heart of the hydraulic system, ensuring a continuous flow of fluid to meet the operational requirements.
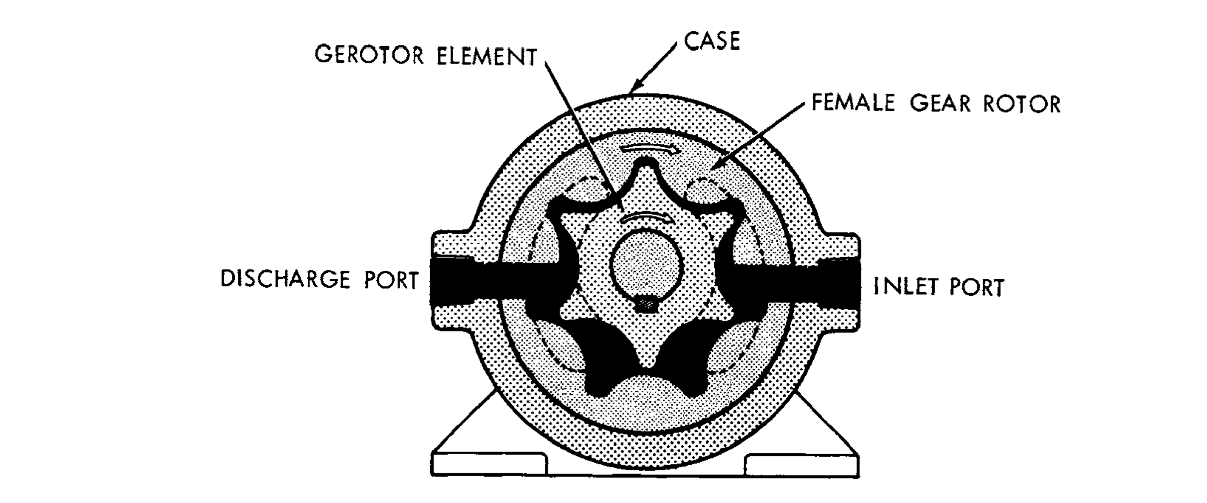
There are different types of hydraulic pumps used in dump applications, each with its own working principles and characteristics. These pumps include gear pumps, vane pumps, and piston pumps, which we will explore in detail in the subsequent sections. Understanding the role of hydraulic pumps and their relationship with other system components is essential for optimizing system performance and efficiency.
Types of Dump Hydraulic Pumps
Dump hydraulic pumps are available in various types, each offering distinct advantages and limitations. Understanding these pump types is crucial for selecting the most suitable option based on specific application requirements. Let’s explore the three main types of dump hydraulic pumps:
- Gear Pumps: Gear pumps are widely used in dump hydraulic systems due to their simplicity and cost-effectiveness. These pumps consist of two meshing gears that create chambers to trap and transport fluid. They are known for their compact size, high reliability, and smooth operation. However, gear pumps may have limitations in handling high pressures and can be sensitive to fluid contamination.
- Vane Pumps: Vane pumps utilize a set of vanes that slide in and out of slots within a rotor, creating chambers for fluid transport. They offer excellent volumetric efficiency, making them suitable for applications requiring high flow rates. Vane pumps are also relatively quiet and provide consistent performance. However, they may have limitations in handling high pressures and can be prone to wear in demanding operating conditions.
- Piston Pumps: Piston pumps are known for their exceptional efficiency and ability to handle high pressures. They employ reciprocating pistons or plungers to generate fluid flow. These pumps can deliver precise control and are commonly used in heavy-duty applications. However, piston pumps tend to be more complex and expensive than gear or vane pumps, and they require careful maintenance to ensure optimal performance.
Each type of dump hydraulic pump has its own advantages and considerations. By understanding their working principles and characteristics, one can make an informed decision when selecting the appropriate pump for specific applications.
Configurations of Dump Hydraulic Pumps
Dump hydraulic pumps can be classified into different configurations based on their operational characteristics and design. Understanding these configurations is essential for choosing the most suitable pump for a particular application. Let’s explore three common configurations of dump hydraulic pumps:
- Single-Acting Pumps: Single-acting pumps are designed to provide hydraulic power in one direction. They deliver fluid flow and pressure during the pump’s forward stroke or actuation. These pumps are commonly used in applications where the hydraulic cylinder or actuator operates in a single direction, such as dump truck hoists or tailgate lifts. Single-acting pumps are relatively straightforward in design and offer cost-effective solutions for applications that do not require bidirectional operation.
- Double-Acting Pumps: Double-acting pumps are designed to deliver hydraulic power in both directions. They provide fluid flow and pressure during both the forward and return strokes of the pump. These pumps are widely used in applications where the hydraulic cylinder or actuator needs to move in both directions, such as dump truck cylinders or hydraulic presses. Double-acting pumps offer enhanced versatility and flexibility compared to single-acting pumps, allowing for more complex hydraulic operations.
- Variable Displacement Pumps: Variable displacement pumps provide the ability to adjust the output flow rate and pressure according to the system’s requirements. These pumps are designed to vary the volume of fluid displaced per revolution or stroke, allowing for precise control of hydraulic power. Variable displacement pumps are commonly used in dump applications where varying loads or operating conditions demand adjustable fluid output. They offer the advantage of optimized energy consumption and improved system efficiency.
Choosing the appropriate pump configuration depends on the specific application’s needs, including the required direction of operation, load demands, and control requirements. Understanding the characteristics and capabilities of each configuration is essential for achieving optimal performance and efficiency in dump hydraulic systems.
Selection Criteria for Dump Hydraulic Pumps
Selecting the right dump hydraulic pump is crucial for ensuring efficient and reliable operation of hydraulic systems. Several key factors should be considered when choosing a pump for a specific application. Let’s explore the important selection criteria for dump hydraulic pumps:
- Flow Rate Requirements: The flow rate, measured in gallons per minute (GPM), determines the amount of hydraulic fluid needed to operate the system effectively. Consider the flow rate requirements of your application, including the maximum and minimum flow rates, to select a pump that can deliver the necessary fluid volume.
- Pressure Considerations: The operating pressure of the hydraulic system is a critical parameter to consider. It determines the pump’s ability to generate sufficient pressure to meet the application’s demands. Evaluate the maximum and minimum pressure requirements of the system and choose a pump that can provide the desired pressure range.
- System Compatibility: Ensure that the selected pump is compatible with the hydraulic system. Consider factors such as fluid compatibility, size, mounting options, and connection requirements. The pump should seamlessly integrate with the existing system components for efficient operation.
- Efficiency and Performance: Assess the pump’s efficiency and performance characteristics. Look for pumps with high volumetric efficiency to minimize energy losses and maximize power output. Consider factors such as speed, horsepower, and overall efficiency to ensure optimal performance.
- Reliability and Durability: Choose a pump known for its reliability and durability. Consider factors such as the pump’s construction, materials used, and reputation of the manufacturer. A reliable pump will ensure consistent operation and reduce the risk of unexpected downtime.
- Cost Considerations: Evaluate the initial cost as well as long-term costs associated with the pump, including maintenance, repair, and energy consumption. Find a balance between cost and performance to select a pump that offers the best value for your specific application.
By considering these selection criteria, you can identify a dump hydraulic pump that meets the requirements of your application, ensuring efficient and reliable operation of your hydraulic system.
Key Factors Influencing Pump Selection
When selecting a dump hydraulic pump, several key factors come into play, influencing the overall performance, reliability, and compatibility with the hydraulic system. Consider the following factors during the pump selection process:
- Environmental Factors: Evaluate the environmental conditions in which the pump will operate. Factors such as temperature variations, humidity levels, and the presence of corrosive or abrasive substances can impact the pump’s performance and longevity. Choose a pump that can withstand the specific environmental conditions of your application.
- Noise and Vibration Considerations: Noise and vibration can affect both the pump’s performance and operator comfort. Some applications may require pumps with low noise levels or dampening mechanisms to minimize vibration. Consider the noise and vibration requirements of your application, especially if it involves close proximity to operators or sensitive equipment.
- Maintenance and Reliability: Assess the maintenance requirements and reliability of the pump. Consider factors such as ease of maintenance, availability of spare parts, and the manufacturer’s reputation for producing reliable pumps. Opt for a pump that is easy to maintain and has a track record of dependable performance to minimize downtime and maximize productivity.
- Efficiency and Energy Consumption: Energy efficiency is an important consideration for both economic and environmental reasons. Look for pumps with high efficiency ratings, as they can reduce energy consumption and operating costs. Consider pumps with advanced features such as variable speed drives or load-sensing technology to optimize energy usage.
- System Compatibility: Ensure that the pump is compatible with the overall hydraulic system. Consider factors such as the system’s pressure rating, flow requirements, and compatibility with the hydraulic fluid being used. The pump should be able to work harmoniously with other system components, ensuring efficient fluid transfer and operation.
- Safety Considerations: Evaluate any specific safety requirements of your application. This may include features such as overload protection, pressure relief valves, or safety interlocks. Choose a pump that incorporates the necessary safety features to protect both the equipment and operators.
By taking these key factors into account during the pump selection process, you can choose a dump hydraulic pump that aligns with the specific needs and demands of your application, ensuring optimal performance, reliability, and safety.
Best Practices for Dump Hydraulic Pump Selection and Maintenance
Selecting and maintaining dump hydraulic pumps requires adherence to best practices to ensure optimal performance, longevity, and safety. Here are some key best practices to consider:
- Evaluating Performance Curves and Efficiency: Study the pump’s performance curves provided by the manufacturer. Understand the relationship between flow rate, pressure, and efficiency to select a pump that meets your specific requirements. Choose a pump that operates efficiently within the desired operating range to minimize energy consumption.
- Proper Installation and Alignment Techniques: Follow the manufacturer’s guidelines for pump installation and alignment. Ensure proper alignment of the pump with the drive system to prevent unnecessary wear, noise, and vibration. Properly aligning the pump will optimize its performance and extend its lifespan.
- Routine Maintenance and Inspection: Implement a regular maintenance schedule for the pump. This includes periodic inspection of seals, filters, fluid levels, and overall pump condition. Follow the manufacturer’s recommended maintenance procedures, including fluid changes and filter replacements, to prevent contamination and ensure proper lubrication.
- Troubleshooting and Timely Repairs: Develop a troubleshooting protocol to identify and address any issues promptly. Regularly monitor pump performance, such as unusual noises, leaks, or changes in pressure. Act promptly to address any abnormalities and carry out necessary repairs or replacements to prevent further damage.
- Proper Fluid Selection and Contamination Control: Use the recommended hydraulic fluid specified by the pump manufacturer. Ensure proper filtration and cleanliness of the fluid to prevent contamination, which can damage pump components. Regularly monitor and maintain the fluid cleanliness levels to ensure optimal pump performance.
- Operator Training and Awareness: Train operators on the proper operation and maintenance procedures for the pump. Promote awareness of best practices, such as avoiding overloading the system, operating within specified parameters, and promptly reporting any issues or abnormalities. Well-trained operators can contribute to the overall longevity and performance of the pump.
By following these best practices, you can optimize the selection, installation, and maintenance of dump hydraulic pumps, ensuring their reliable operation, longevity, and efficient performance.
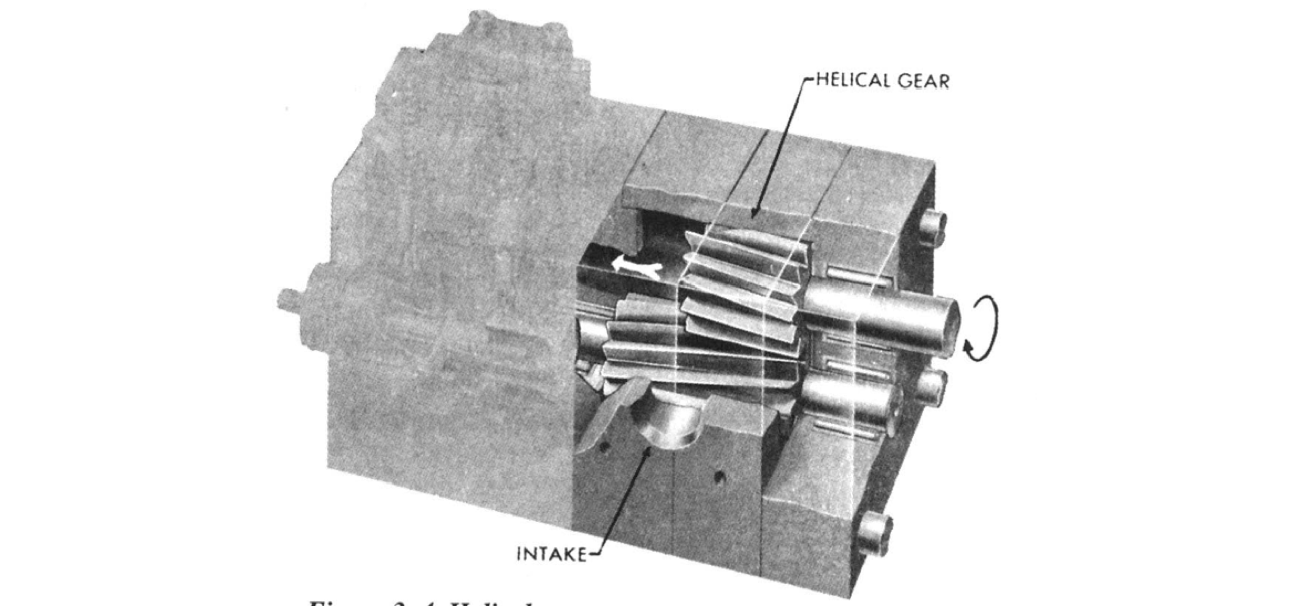
Conclusion
In conclusion, dump hydraulic pumps play a crucial role in various industries, powering the movement of hydraulic fluids and enabling the operation of heavy machinery and equipment. By understanding the different types of dump hydraulic pumps, their configurations, and the selection criteria, you can make informed decisions to choose the most suitable pump for your specific application.
Gear pumps, vane pumps, and piston pumps offer different advantages and limitations, allowing you to select the pump that best aligns with your requirements. Consider factors such as flow rate, pressure, system compatibility, and efficiency when making your choice.
Moreover, key factors such as environmental conditions, noise and vibration considerations, and maintenance and reliability should be taken into account to ensure optimal pump performance. Adhering to best practices such as evaluating performance curves, proper installation and alignment, routine maintenance, and troubleshooting techniques will contribute to the longevity and efficiency of the pump.

By considering these aspects and making informed decisions, you can optimize the selection and maintenance of dump hydraulic pumps, leading to improved productivity, minimized downtime, and enhanced overall performance of hydraulic systems.
Related Keywords
# Dump Trailer Hydraulic Cylinder,
# Heavy Duty 12 Volt Hydraulic Pump,
# 12V Double Acting Hydraulic Pump,
# Hydraulic Pump for Dump Trailer near me,
# 12V Hydraulic Pump and Ram,
# KTI Hydraulic Pump Manual,