Hydraulic pump manufacturers play a crucial role in providing essential equipment for hydraulic systems. These manufacturers specialize in designing, manufacturing, and supplying hydraulic pumps that are integral to a wide range of industries. Ensuring the quality and reliability of hydraulic pumps is of utmost importance for optimal performance and system longevity. In this content, we will define hydraulic pump manufacturers and emphasize the significance of quality and reliability in their manufacturing processes. We will also provide an overview of the key factors to consider when selecting a reliable hydraulic pump manufacturer. By understanding these factors, businesses can make informed decisions and choose manufacturers that prioritize quality and reliability in their hydraulic pump systems.
Understanding Hydraulic Pump Quality
When evaluating hydraulic pump manufacturers, understanding the concept of quality is essential. Let’s explore the definition of quality in the context of hydraulic pumps, the factors that contribute to a high-quality hydraulic pump, and the importance of quality control and testing in the manufacturing processes.
- Definition of Quality: In the context of hydraulic pumps, quality refers to the ability of a pump to consistently meet or exceed performance specifications, withstand operating conditions, and deliver reliable and efficient fluid power. A high-quality hydraulic pump exhibits durability, precision, and optimal functionality throughout its lifespan.
- Factors Contributing to High-Quality Hydraulic Pumps:a. Materials: The selection of high-quality materials is crucial for manufacturing reliable hydraulic pumps. Premium-grade metals, alloys, and specialized coatings enhance durability, corrosion resistance, and overall performance.b. Design: Well-engineered designs consider factors such as flow rates, pressure ratings, sealing mechanisms, and efficiency. A properly designed hydraulic pump optimizes performance, minimizes energy losses, and reduces wear and tear.c. Manufacturing Processes: Advanced manufacturing processes, such as precision machining, computerized control systems, and stringent quality control protocols, contribute to the production of high-quality hydraulic pumps. Attention to detail and adherence to industry standards ensure consistency and reliability.d. Testing and Inspection: Rigorous testing and inspection procedures are integral to ensuring the quality of hydraulic pumps. Thorough performance tests, pressure tests, and quality checks verify that each pump meets the specified requirements and performs reliably under operating conditions.
- Importance of Quality Control and Testing:a. Consistency: Effective quality control measures ensure consistent manufacturing processes and adherence to specifications. This minimizes variations in pump performance, enhances reliability, and promotes system efficiency.b. Reliability: Quality control and testing help identify any potential defects or flaws in the manufacturing process, ensuring that only reliable pumps are delivered to customers. This reduces the risk of pump failures, downtime, and costly repairs.c. Customer Satisfaction: High-quality hydraulic pumps provide customers with confidence in their investment. By delivering reliable performance and minimizing maintenance requirements, manufacturers can enhance customer satisfaction and build long-term relationships.d. Compliance with Standards: Quality control and testing ensure that hydraulic pumps meet industry standards, regulations, and safety requirements. Manufacturers who adhere to these standards demonstrate their commitment to producing safe and reliable products.
Understanding hydraulic pump quality is crucial when comparing manufacturers. By considering the factors contributing to high-quality pumps and evaluating manufacturers’ quality control processes and testing procedures, businesses can select manufacturers that prioritize delivering reliable, efficient, and durable hydraulic pumps.
Testing and Certification Standards
When comparing hydraulic pump manufacturers, it is important to consider the testing and certification standards they adhere to. Let’s explore an overview of industry-standard testing and certification processes, recognized certifications for hydraulic pump manufacturers, and how to evaluate a manufacturer’s adherence to quality standards.
- Overview of Testing and Certification Processes:a. Performance Testing: Performance testing involves evaluating the hydraulic pump’s ability to meet specified performance parameters such as flow rate, pressure ratings, and efficiency. These tests ensure that the pump performs as intended and meets the required performance criteria.b. Pressure Testing: Pressure testing assesses the hydraulic pump’s ability to withstand the designated operating pressures without leaks or failures. It verifies the pump’s structural integrity and ensures its reliability under pressure.c. Endurance Testing: Endurance testing involves subjecting the hydraulic pump to extended operating conditions to simulate real-world usage. This test assesses the pump’s durability, performance consistency, and resistance to wear and fatigue.d. Environmental Testing: Environmental testing evaluates the pump’s performance and reliability under various environmental conditions, such as temperature extremes, humidity, vibration, and exposure to contaminants. It ensures the pump can operate reliably in diverse environments.
- Recognized Certifications for Hydraulic Pump Manufacturers:a. ISO 9001: The ISO 9001 certification demonstrates a manufacturer’s commitment to quality management systems. It ensures that the manufacturer follows standardized processes, continuous improvement practices, and meets customer expectations.b. ISO 14001: The ISO 14001 certification signifies a manufacturer’s commitment to environmental management practices. It demonstrates their adherence to eco-friendly manufacturing processes and sustainability initiatives.c. CE Marking: CE marking indicates that the hydraulic pump manufacturer complies with European Union safety, health, and environmental protection standards. It demonstrates the pump’s conformity to applicable regulations and requirements.d. UL Certification: UL certification is a safety certification provided by Underwriters Laboratories. It ensures that the hydraulic pump meets specific safety standards and requirements for reliable operation.
- Evaluating Adherence to Quality Standards:a. Research and Documentation: Review the manufacturer’s website, product literature, and technical documentation to identify any claims of adherence to industry standards and certifications. Look for evidence of their commitment to quality and compliance.b. Certifications and Compliance Statements: Request information about the certifications and standards the manufacturer adheres to. Assess the validity and relevance of these certifications to the hydraulic pump industry.c. Testing and Quality Control Processes: Inquire about the manufacturer’s testing and quality control processes. A reputable manufacturer will have well-defined processes in place and will be transparent about their quality control measures.d. Independent Verification: Consider engaging with independent third-party organizations that verify and certify hydraulic pump manufacturers. These organizations provide unbiased assessments of a manufacturer’s adherence to quality standards.
Evaluating a hydraulic pump manufacturer‘s adherence to testing and certification standards is crucial for ensuring the reliability and quality of their products. By considering recognized certifications, evaluating their testing and quality control processes, and seeking independent verification, businesses can select manufacturers that prioritize the highest standards of quality in their hydraulic pump manufacturing processes.
Materials and Manufacturing Processes
When comparing hydraulic pump manufacturers, it is essential to consider the materials used and the manufacturing processes employed. Let’s explore the importance of using high-quality materials in hydraulic pump manufacturing, an overview of advanced manufacturing processes for hydraulic pumps, and the impact of material selection and manufacturing techniques on reliability.
- Importance of Using High-Quality Materials:a. Durability and Longevity: High-quality materials, such as premium-grade metals and alloys, offer superior durability and longevity. These materials can withstand the demanding operating conditions of hydraulic systems, including high pressures, temperature fluctuations, and corrosive environments.b. Performance Optimization: The choice of materials directly influences the pump’s performance. Materials with excellent wear resistance and low friction properties minimize energy losses and optimize pump efficiency. This results in improved overall system performance and reduced operational costs.c. Corrosion Resistance: Hydraulic pumps may be exposed to various fluids and environments that can cause corrosion. Using materials with high corrosion resistance, such as stainless steel or specialized coatings, ensures the pump’s reliability and longevity, even in harsh operating conditions.
- Advanced Manufacturing Processes for Hydraulic Pumps:a. Precision Machining: Precision machining techniques, such as computer numerical control (CNC) machining, ensure the accurate production of complex pump components. CNC machining allows for tight tolerances, consistent dimensions, and precise surface finishes, resulting in reliable and high-performance hydraulic pumps.b. Computer-Aided Design (CAD): CAD software enables manufacturers to design hydraulic pumps with intricate geometries and optimize their performance. It allows for virtual testing and simulation to ensure optimal design parameters, enhancing reliability and efficiency.c. Automated Assembly: Automated assembly processes ensure consistent and precise assembly of hydraulic pump components. Automated systems reduce the risk of human errors, improve efficiency, and maintain strict quality control throughout the assembly process.d. Quality Control Measures: Advanced manufacturing processes incorporate rigorous quality control measures at various stages of production. This includes inspection and testing of raw materials, intermediate components, and final assembled pumps to verify compliance with specifications and quality standards.
- Impact of Material Selection and Manufacturing Techniques:a. Reliability and Performance: The choice of materials directly affects the pump’s reliability and performance. High-quality materials provide enhanced resistance to wear, corrosion, and fatigue, resulting in reliable operation and extended service life.b. Efficiency and Energy Optimization: Optimal material selection and manufacturing processes contribute to improved pump efficiency. Well-designed hydraulic pumps with optimized materials and manufacturing techniques minimize energy losses, reduce friction, and increase overall system efficiency.c. Maintenance and Repair: The use of high-quality materials simplifies maintenance and repair processes. Components made from durable materials are less prone to damage and require less frequent replacement, reducing downtime and maintenance costs.d. Product Consistency: Consistent material quality and manufacturing processes ensure that each hydraulic pump produced meets the same high standards. This results in consistent product performance, allowing for easy integration and replacement within existing hydraulic systems.
Selecting a hydraulic pump manufacturer that utilizes high-quality materials and employs advanced manufacturing processes is vital for ensuring reliable and efficient hydraulic pump systems. By considering the impact of material selection, evaluating the manufacturer’s manufacturing techniques, and prioritizing reliability and performance, businesses can choose manufacturers that deliver durable, high-performance hydraulic pumps for their specific application needs.
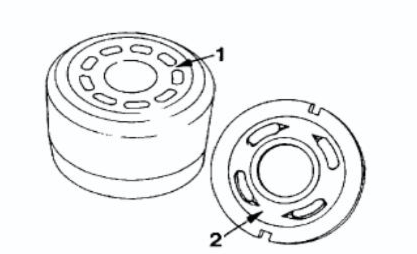
Product Design and Engineering
The product design and engineering of hydraulic pumps play a significant role in their performance, efficiency, and reliability. When comparing hydraulic pump manufacturers, it is crucial to consider the significance of well-designed pump systems, the key considerations in hydraulic pump engineering, and how to evaluate a manufacturer’s expertise in product design and engineering.
- Significance of Well-Designed Hydraulic Pump Systems:a. Optimal Performance: Well-designed hydraulic pump systems maximize performance by ensuring efficient fluid flow, precise control, and minimal energy losses. The design considers factors such as flow rates, pressure ratings, and volumetric efficiency to deliver the desired output for specific applications.b. System Integration: A well-designed hydraulic pump integrates seamlessly with the overall hydraulic system. Compatibility with other components, such as valves, actuators, and control systems, ensures smooth operation and optimal system performance.c. Reliability and Durability: A robust design with proper consideration for materials, stress analysis, and structural integrity enhances the pump’s reliability and durability. It minimizes the risk of failures, leaks, and premature wear, resulting in a longer service life and reduced maintenance requirements.
- Considerations in Hydraulic Pump Engineering:a. Fluid Compatibility: Hydraulic pumps need to be designed to handle the specific fluid being used in the system. Different fluids may have varying viscosities, temperatures, and chemical properties, requiring specific design considerations to ensure compatibility and optimal performance.b. Efficiency and Energy Optimization: Hydraulic pump engineering focuses on maximizing efficiency to minimize energy consumption and reduce operating costs. This includes optimizing pump design for higher volumetric and mechanical efficiencies, reducing internal leakage, and minimizing pressure drops.c. Noise and Vibration Control: Effective engineering design techniques help mitigate noise and vibration levels associated with hydraulic pump operation. Proper component selection, alignment, and damping measures contribute to a quieter and smoother operation, improving operator comfort and system performance.d. Serviceability and Maintenance: Design considerations for serviceability and maintenance facilitate easier access to components, simplifying inspection, repair, and routine maintenance tasks. Well-designed hydraulic pumps reduce downtime and maintenance costs by minimizing the time and effort required for servicing.
- Evaluating Manufacturer’s Expertise in Design and Engineering:a. Research and Documentation: Research the manufacturer’s website, product documentation, and technical resources to assess their focus on product design and engineering. Look for information highlighting their expertise, design capabilities, and innovative solutions.b. Industry Experience and Track Record: Consider the manufacturer’s industry experience and track record in delivering well-designed hydraulic pump systems. Evaluate their success stories, case studies, and customer testimonials related to design and engineering excellence.c. Collaboration and Customization: Assess the manufacturer’s willingness to collaborate and customize hydraulic pump solutions based on specific application requirements. A manufacturer that actively engages in understanding customer needs and provides tailored solutions demonstrates their engineering expertise.d. R&D and Innovation: Evaluate the manufacturer’s investment in research and development (R&D) and commitment to innovation. Manufacturers that prioritize R&D often introduce new technologies, materials, and design improvements that enhance the performance and efficiency of their hydraulic pumps.
Selecting a hydraulic pump manufacturer with expertise in product design and engineering is crucial for achieving optimal performance, reliability, and efficiency. By considering the significance of well-designed pump systems, evaluating engineering considerations, and assessing a manufacturer’s expertise in design and engineering, businesses can choose manufacturers that prioritize delivering high-quality and innovative hydraulic pump solutions for their specific application needs.
Quality Assurance and Control Measures
Implementing quality assurance and control measures is vital in hydraulic pump manufacturing to ensure consistent product quality, reliability, and customer satisfaction. When comparing hydraulic pump manufacturers, it is essential to understand the significance of quality assurance practices, the importance of implementing quality control measures throughout the production process, and ensuring consistency and reliability through rigorous quality checks.
- Overview of Quality Assurance Practices:a. Standardized Processes: Implementing standardized processes throughout the manufacturing cycle ensures consistency and adherence to quality standards. These processes encompass design, material selection, manufacturing, assembly, testing, and inspection stages.b. Quality Management Systems: Quality management systems, such as ISO 9001, establish a framework for implementing quality assurance practices. They define processes, responsibilities, and procedures to ensure compliance with quality standards, continuous improvement, and customer satisfaction.c. Documentation and Record-Keeping: Maintaining accurate documentation and records of all stages of the manufacturing process is essential for quality assurance. This includes design specifications, material certifications, inspection reports, test results, and production data, facilitating traceability and accountability.
- Importance of Quality Control Measures:a. Incoming Materials Inspection: Conducting thorough inspections of incoming materials, including raw materials and purchased components, ensures compliance with specified standards and eliminates the risk of using substandard or non-conforming materials.b. In-Process Quality Control: Implementing quality control measures at various stages of the manufacturing process allows for real-time monitoring and identification of any deviations or defects. This enables prompt corrective actions and minimizes the potential for non-conforming products.c. Final Inspection and Testing: Rigorous final inspection and testing procedures verify that each hydraulic pump meets the specified requirements and performance standards. These include functional testing, pressure testing, dimensional checks, and performance verification.d. Statistical Process Control: Statistical process control techniques can be employed to monitor and analyze production data, identifying trends, patterns, and potential process variations. This allows for proactive measures to maintain consistent quality and identify areas for improvement.
- Ensuring Consistency and Reliability:a. Calibration and Maintenance: Regular calibration and maintenance of testing equipment and machinery ensure accurate and reliable measurements. Properly calibrated equipment contributes to reliable quality checks and consistent product quality.b. Training and Skill Development: Providing comprehensive training to manufacturing personnel on quality control processes, techniques, and product specifications is crucial. Skilled and trained employees understand the importance of quality and contribute to maintaining consistent manufacturing standards.c. Continuous Improvement: Embracing a culture of continuous improvement fosters ongoing enhancements in quality control and manufacturing processes. Regular evaluation, analysis of feedback, and implementation of corrective actions drive product quality improvements and customer satisfaction.d. Supplier Quality Management: Implementing robust supplier quality management processes ensures that purchased components and materials meet specified quality requirements. Regular evaluations, audits, and collaboration with suppliers contribute to consistent product quality.
By implementing effective quality assurance practices, employing stringent quality control measures, and ensuring consistency and reliability through rigorous inspections and testing, hydraulic pump manufacturers can deliver products that meet or exceed customer expectations. Businesses should evaluate manufacturers based on their commitment to quality assurance and control, certifications obtained, and their ability to consistently deliver high-quality hydraulic pumps.
In the next segment, we will explore the significance of warranty coverage and after-sales support when comparing hydraulic pump manufacturers, along with the importance of evaluating a manufacturer’s commitment to customer satisfaction.
Warranty and After-sales Support
When comparing hydraulic pump manufacturers, it is crucial to consider the warranty coverage and after-sales support they provide. Let’s explore the importance of warranty coverage in hydraulic pump manufacturers, how to evaluate a manufacturer’s warranty policies and support, and the availability of after-sales support for maintenance and repairs.
- Importance of Warranty Coverage:a. Protection and Assurance: Warranty coverage provides protection and assurance to customers, ensuring that their investment in a hydraulic pump is supported. A comprehensive warranty demonstrates the manufacturer’s confidence in their product’s quality and reliability.b. Risk Mitigation: Warranty coverage mitigates the risk of potential defects or failures in the hydraulic pump. If any issues arise within the warranty period, customers can receive necessary repairs, replacements, or refunds, minimizing financial risks and downtime.c. Long-term Relationship: A manufacturer that offers a strong warranty program builds trust and establishes a long-term relationship with customers. It demonstrates the manufacturer’s commitment to customer satisfaction and confidence in the longevity of their hydraulic pump.
- Evaluating Warranty Policies and Support:a. Warranty Duration: Consider the duration of the manufacturer’s warranty coverage. A longer warranty period provides extended protection and peace of mind. However, also assess the warranty terms and any exclusions or limitations that may be associated with it.b. Coverage Details: Evaluate the specifics of the warranty coverage. Understand what components and issues are covered, as well as any conditions or limitations. A comprehensive warranty should cover major components, manufacturing defects, and ensure hassle-free support.c. Warranty Claims Process: Review the manufacturer’s warranty claims process. A manufacturer with a streamlined and transparent claims process ensures that customers can easily submit and track warranty claims, leading to efficient resolutions.d. After-sales Support: Inquire about the manufacturer’s after-sales support. A reputable manufacturer should provide technical assistance, guidance, and expertise for maintenance, troubleshooting, and repairs. Prompt and knowledgeable support contributes to the smooth operation and longevity of the hydraulic pump.
- Availability of After-sales Support for Maintenance and Repairs:a. Technical Assistance: Evaluate the manufacturer’s provision of technical assistance beyond the warranty period. Reliable manufacturers should offer ongoing technical support to address any operational or maintenance queries that customers may have.b. Spare Parts Availability: Inquire about the availability of spare parts for the hydraulic pump. A manufacturer with readily available spare parts ensures quick and efficient repairs, minimizing system downtime and reducing overall maintenance costs.c. Training and Documentation: Consider whether the manufacturer provides training programs or documentation to support customers in the maintenance and repair of their hydraulic pumps. These resources empower operators and maintenance personnel to perform routine tasks effectively and prolong the pump’s lifespan.d. Commitment to Customer Satisfaction: Evaluate the manufacturer’s commitment to customer satisfaction through their after-sales support. Positive customer feedback, testimonials, and a reputation for excellent customer service indicate a manufacturer’s dedication to ensuring customer success and satisfaction.
By considering the warranty coverage, evaluating warranty policies and support, and assessing the availability of after-sales support for maintenance and repairs, businesses can choose hydraulic pump manufacturers that prioritize customer satisfaction, offer peace of mind, and provide ongoing support throughout the lifecycle of the hydraulic pump.
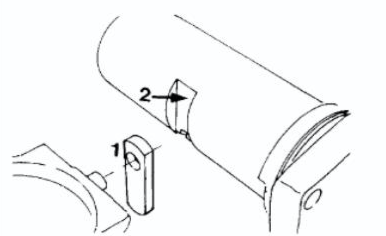
In the final segment, we will recap the importance of quality and reliability in hydraulic pump manufacturing, summarize the key considerations when comparing manufacturers, and discuss the implications for industries relying on high-quality hydraulic pump systems.
Conclusion
In conclusion, the importance of quality and reliability in hydraulic pump manufacturing cannot be overstated. When comparing hydraulic pump manufacturers, it is crucial to consider various factors to make an informed decision. Let’s recap the key factors to consider and their implications for selecting a reliable hydraulic pump manufacturer.
- Importance of Quality and Reliability: Quality and reliability are essential for ensuring the optimal performance, durability, and efficiency of hydraulic pump systems. Selecting a manufacturer that prioritizes these aspects ensures long-term success and minimizes operational disruptions.
- Key Considerations:a. Thorough Evaluation: Conduct a thorough evaluation of hydraulic pump manufacturers, considering factors such as quality control, testing, certifications, materials, design, engineering, and customer support.b. Adherence to Standards: Assess the manufacturer’s adherence to industry standards, certifications, and quality management systems such as ISO 9001. These demonstrate their commitment to meeting stringent quality requirements.c. Expertise and Innovation: Evaluate the manufacturer’s expertise in design, engineering, and innovation. Manufacturers with a track record of delivering innovative solutions and continuous improvement demonstrate their commitment to excellence.d. Warranty and After-sales Support: Consider the warranty coverage, claims process, and availability of after-sales support. A comprehensive warranty and reliable after-sales support contribute to customer satisfaction and system longevity.
- Implications for Industries: Selecting a reliable hydraulic pump manufacturer has implications for industries relying on high-quality hydraulic pump systems. It ensures consistent performance, minimizes downtime, reduces maintenance costs, and supports efficient operations.
By considering these factors and their implications, businesses can make informed decisions, enhance the performance of their hydraulic systems, and establish successful long-term partnerships with reliable hydraulic pump manufacturers.
In summary, choosing the right hydraulic pump manufacturer involves a comprehensive evaluation of factors such as quality, reliability, adherence to standards, expertise, warranty coverage, and after-sales support. By considering these factors, businesses can mitigate risks, optimize system performance, and select manufacturers that meet their specific hydraulic pump requirements.
We have covered the key considerations when comparing hydraulic pump manufacturers throughout this content. Thorough evaluation of these factors, including the importance of quality and reliability, understanding pump types, evaluating testing and certification standards, considering materials and manufacturing processes, assessing product design and engineering, implementing quality assurance and control measures, and ensuring warranty coverage and after-sales support, will guide businesses in selecting the most suitable manufacturer for their specific hydraulic pump needs.
By considering these factors and their implications, businesses can make informed decisions, enhance the performance of their hydraulic systems, and establish successful long-term partnerships with reliable hydraulic pump manufacturers.
Related Keywords
# Hydraulic Gear Pump manufacturers,
# Hydraulic pump details,
# Parker Hydraulic Pump,
# Top 10 hydraulic companies in world,
# Danfoss hydraulic pump,
# Hydraulic Oil Pump,
# Types of hydraulic pumps PDF,
# Eaton hydraulic pump,